After a four-year ambitious challenge, the EU-funded MultiFAL project is entering its final phase with excellent results for the aeronautical assembly industry: the development of a full size automated plant system for joining thermoplastic fuselage shells that accommodates the existing assembly plant system at the topic managers’ facility.
Led by CT and incorporating the expertise of FFT and AIMEN, this initiative will contribute to reducing the commissioning time of automated plant systems up to 20% by using virtual commissioning tools. It will also help increase the level of detail for production steps by around 25% by implementing interfaces between plant system and production control.
CT has been responsible for the design and final testing of the fuselage demonstrator. The implementation of 3DEXPERIENCE on a cloud platform has been crucial to ensure quick and easy collaboration between all partners (designers, managers and external suppliers) for the storage, creation and exchange of all project information: design files, from concept designs in CATIA V5 to final 3D environment in CATIA 3DEXPERIENCE, manufacturing drawings and documentation in a wide range of file formats. The platform was also used for project management activities, such as assigning tasks, defining deadlines and releasing components for the final design review.
All in all, MultiFAL implements process simulation, automation, plant concepts and virtual commissioning technologies in order to improve assembly process performance and provide a deep understanding of the relevant factors involved in implementing a full size automated plant following a brownfield approach. Different assembly approaches and joining processes for different use-cases have been considered, taking into account the currently existing double-sided and limited accessibility for full fuselage sections. As a result, MultiFAL also facilitates the adaptability of both the robotic machinery and a central control system.
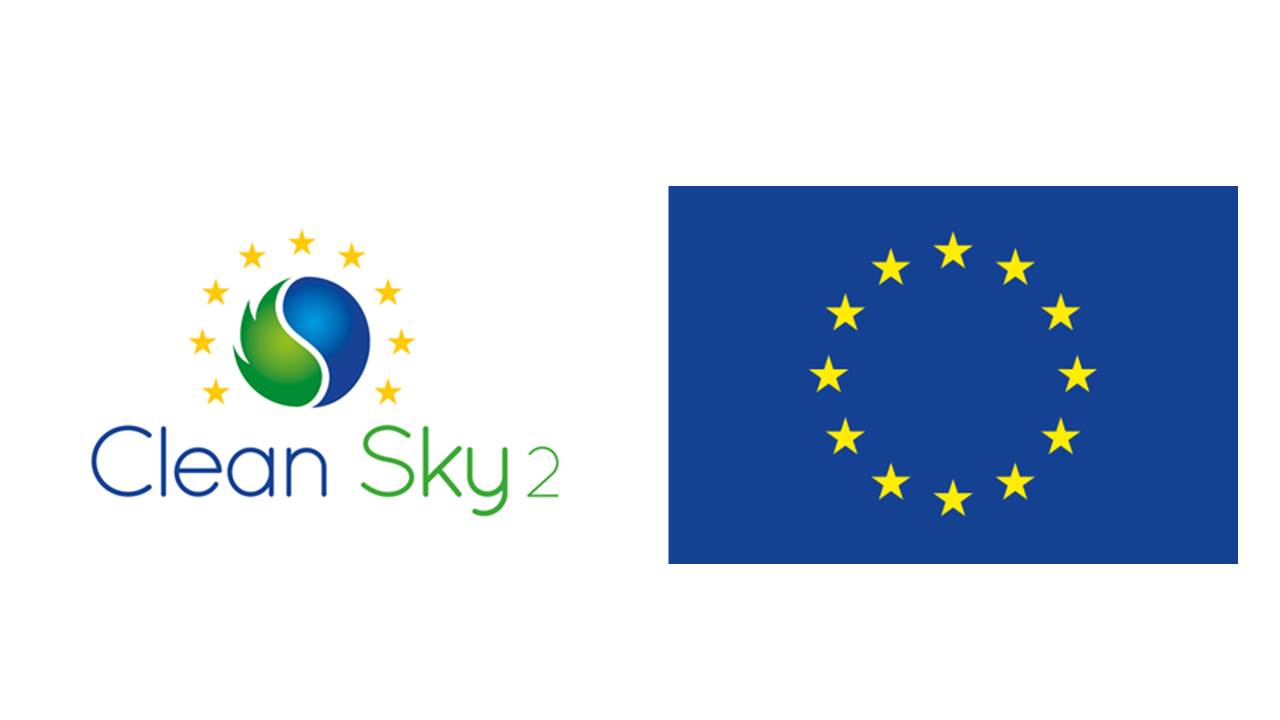