The REMEDI R&D project seeks to overcome some of the barriers currently associated with the aspects of design optimization and productivity in the digital manufacture of medium-large components with high added value, manufactured using laser metal deposition technologies, in order to improve the industry’s acceptance of this technology. The value chain of these processes is made up of the phases of design, process configuration, process planning, manufacturing with online control/monitoring, post-processing, and quality control, and it is precisely the redesign phase that really offers the greatest added value and the greatest benefits. REMEDI also focuses on using those different manufacturing stages to provide feedback on the design itself, until it reaches its most efficient optimization.
Based on the industry’s need for this emerging technology, REMEDI is aimed precisely at defining the design methodology for Laser Metal Deposition (LMD) processes with the goal of reducing the significant consequences of the design on the final quality of the piece.
To implement the concept of Quality-by-Design (QBD) in the manufacture of the prototypes of the project, a software/hardware platform consisting of an offline engineering unit, which integrated different commercial CAx technologies and a physical additive manufacturing facility by LMD under the same layer, was used to implement and validate a Quality-by-Design methodology for the additive manufacturing of large components optimised to achieve zero defects.
This environment has been implemented in two manufacturing facilities (a Spanish factory, Smarmec and a Turkish factory, Coskunoz R&D), to demonstrate the concept and obtain future reproducibility in any industry that requires it. The REMEDI technology is being validated for two different sectors that demand high value-added components: space applications and aircraft components.
The project has passed several technological milestones in reaching its goals:
- Topological optimisation of parts design based on structural integrity requirements and functional loads, to provide a more efficient component in terms of raw material usage, production cost and delivery time.
- Establish the manufacturability capabilities of the LMD process in its different configurations of equipment parameters/process parameters, in order to feed the Topological Optimisation tool with data from real industrial scenarios.
- Improve the configuration cycle of the system/deposition strategies/multiphysical simulation to achieve a thermal balance, which would serve at the same time to automatically evaluate the design of the piece obtained in the previous steps, detecting areas of the piece that could complicate its manufacture or the final functionality of the piece.
- Analyse the data associated with the laser power and the temperature of the molten bath at any point of the process path using monitoring systems, to connect them to the design stage and propose new design changes based on this.
About REMEDI
The REMEDI project will run for 30 months (it is expected to end in 2021) and has an approximate budget of €2M. The international project was approved under the SMART EUREKA Advanced Manufacturing call for projects. Nationally, the project is subsidised by the CDTI through the INNOGLOBAL 2018 program, and supported by the Ministry of Science and Innovation, with a total budget of €1,335,516.00, and €392,657.00 in total aid.
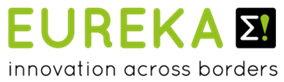
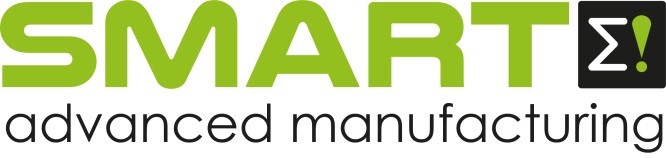
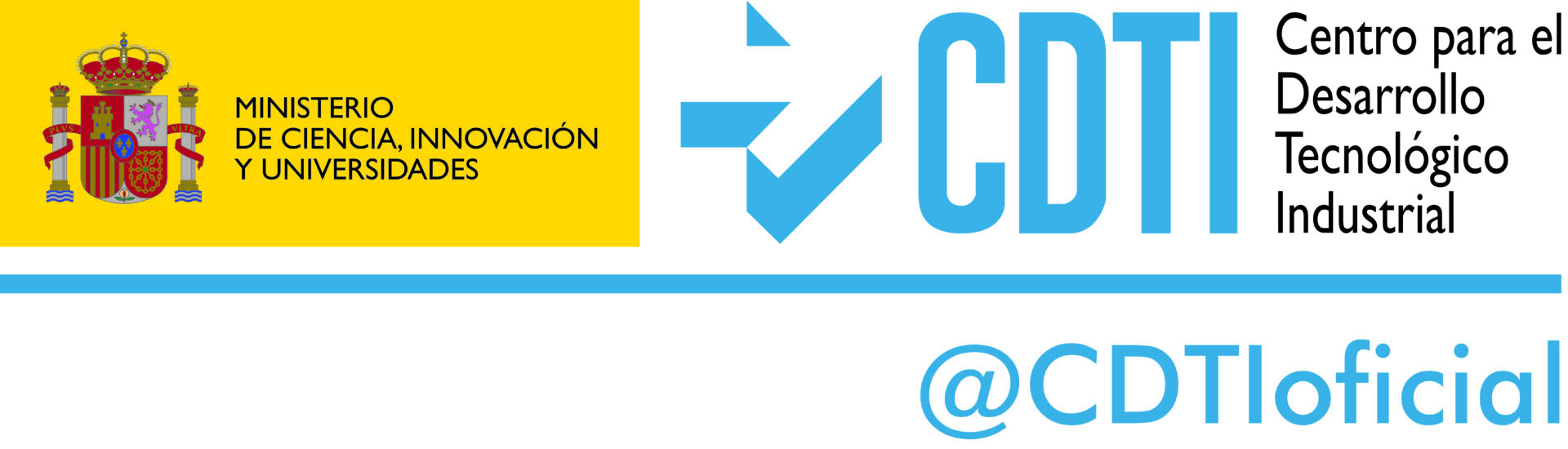